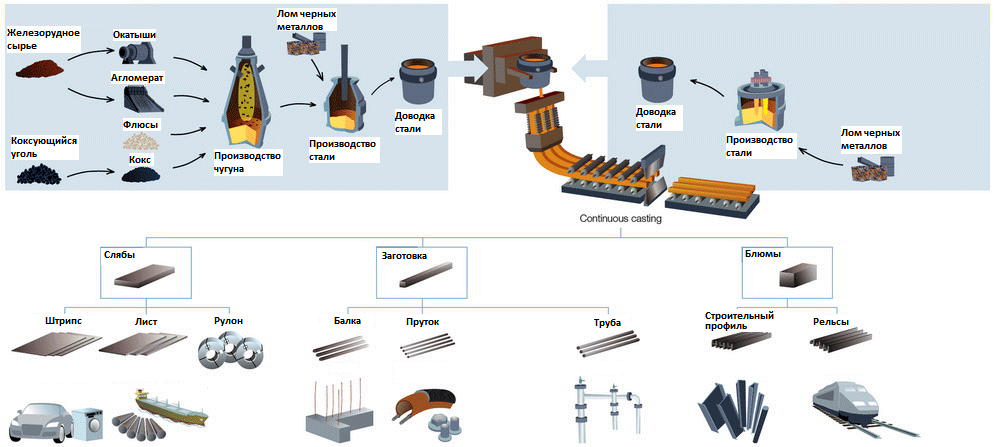
Тенденции развития современной металлургии и новые процессы получения железа
Мартеновский процесс, долгое время державший монополию в области производства стали, уступил в конце 60-х годов XX века место более производительному кислородно-конвертерному. Дальнейшая борьба шла уже между конвертерным и набирающим силу электросталеплавильным процессом.
-
Дополнительная информация
- Авторы:Неделин Сергей Васильевич
- E-mail:nedelin@gmail.com
Мартеновский процесс, долгое время державший монополию в области производства стали, уступил в конце 60-х годов XX века место более производительному кислородно-конвертерному. Дальнейшая борьба шла уже между конвертерным и набирающим силу электросталеплавильным процессом.
Динамика развития процессов производства стали
Растущий спрос на специальные виды сталей и развитие мини-миллов (небольших прокатных заводов, имеющих в составе электропечи) упрочил позиции этого способа производства стали. Развитие основных процессов производства стали с середины XX века представлено на диаграмме:
Доля мартеновского производства по итогам 2008 года в мире составляла 2,2%. Мартеновское производство сосредоточено в основном в странах СНГ (23,4% от общего производства стали по итогам 2008 года). В связи с закрытием избыточных и малоэффективных производств на фоне мирового финансового кризиса доля мартеновского производства по итогам 2009 года значительно сократилась. Так, на российских предприятиях о закрытии мартеновских цехов объявили Череповецкий МК (Северсталь) и Нижнетагильский МК (Евраз). Таким образом, по итогам 2010 года доля мартеновского производства составляла уже 14,3% в странах СНГ и 1,3% - в мире.
Соотношение между конвертерным и электросталеплавильным процессами в общем объеме производства стали в ближайшей перспективе сохранится: с одной стороны растет количество предприятий неполного цикла (мини-миллы) с использованием электрометаллургии, с другой стороны – ведущий мировой производитель стали Китай наращивает производство именно конвертерной стали (доля кислородно-конвертерной стали в КНР по итогам 2010 года составляет 90,2%).
Основные компоненты металлошихты для сталеплавильных процессов
Компонентами металлошихты для производства стали в общем случае являются чугун, лом черных металлов и металлизованное сырье (Direct Reduction Iron – DRI).
Металлошихта для основных сталеплавильных процессов может варьироваться в довольно широком диапазоне и зависит в большинстве случаев от доступности ресурсов и ценовых соотношений между ними. Так, в периоды роста стоимости железорудного сырья и снижения цен на лом чёрных металлов комбинаты увеличивают использование лома за счёт снижения чугуна и наоборот.
Общее представление о технологических диапазонах изменения сталеплавильной шихты можно получить из следующей таблицы:
Кислородно-конвертерное Электростале-плавильное Мартеновское (скрап-рудный процесс) Мартеновское (скрап процесс)
Кислородно-конвертерное |
Электростале-плавильное |
Мартеновское (скрап-рудный процесс) |
Мартеновское (скрап процесс) |
|
Доля процесса в выплавке стали (мир) |
69,8% |
29,0% |
1,2% |
|
Доля процесса в выплавке стали (СНГ) |
64,6% |
21,1% |
14,3% |
|
Типовая шихта, %: |
||||
-жидкий чугун |
75-80 |
0-30 |
25-55 |
|
-лом черных металлов |
20-25 |
30-100 |
25-75 |
|
-чугун чушковый |
0-5 |
5-15 |
||
-металлизованное сырье |
0-70 |
|||
Максимальная доля лома в металлошихте (технологическое ограничение) |
28% |
100% |
45% |
75% |
Заменители лома |
чугун жидкий* |
чугун жидкий* |
чугун жидкий* |
чугун чушковый |
чугун чушковый* |
чугун чушковый* |
чугун чушковый* |
DRI |
|
DRI |
DRI |
DRI |
Примечание:
* – ограниченное применение
Наибольшая вариативность металлошихты наблюдается в электросталеплавильном производстве. Источником тепла в ЭСП является энергия электрической дуги и необходимость в других теплоносителях отсутствует, что снимает потребность в приходе тепла от компонентов шихты.
Как уже говорилось выше, мартеновский процесс ввиду его незначительной доли в мировом производстве не играет значительной роли в потреблении металлосырья. Таким образом, в общем виде схема классического производства стали выглядит следующим образом:
Преимущества классической схемы:
- высокая степень извлечения железа;
- высокая удельная производительность;
- высокий тепловой КПД;
- эффективный расход энергоресурсов.
Недостатки классической схемы:
- высокие стартовые капитальные затраты при строительстве нового производства;
- необходимость предварительного окускования шихты;
- использование кокса в качестве основного энергоносителя и восстановителя;
- ограниченные ресурсы качественного лома черных металлов.
Новые процессы получения железа
Основные причины возникновения новых процессов получения железа вытекают из недостатков классической схемы: стремление сократить технологическую цепочку и снизить зависимость от использования кокса – основного восстановителя и источника тепла в классической схеме производства стали. Как следствие – в обозначении новых процессов часто используются термины «прямое получение железа» и «бескоксовая металлургия».
По виду производимого полупродукта новые процессы получения железа разделяют на твердофазные и жидкофазные. Доля последних крайне мала (5-6% от всей бескоксовой металлургии) и их полупродукт не может выступать в составе металлошихты в качестве полновесной альтернативы лому.
Исходным сырьём для новых процессов являются железная руда или железорудные окатыши. Таким образом, стадия восстановления (перевод железа из окисленной формы в металлическую) также присутствует и в процессах альтернативной металлургии.
В качестве восстановителя в твердофазных процессах используют продукты конверсии (перевода в CO и H2) природного газа или продукты газификации углей. Вследствие относительно низкой эффективности применение газификации углей ограничено. В последнее время процессы, связанные с газификацией углей, наиболее активно развиваются в Индии.
В жидкофазных процессах основным восстановителем и источником тепла является уголь.
Схема производства стали из металлизованного полупродукта приведена ниже:
Многообразие идей и схем реализации породило множество названий для процессов и продуктов бескоксовой металлургии. Перечислим наиболее употребимые из них:
- DRI – Direct Reduced Iron
- SI, SPI – Sponge Iron
- HBI – Hot Briquetted Iron
- HDRI – Hot Direct Reduced Iron
- CDRI – Cold Direct Reduced Iron
- МП – металлизованный полупродукт
- ЖПВ – железо прямого восстановления
- ЖПП – железо прямого получения
- ПВЖ – прямовосстановленное железо
- ГЖ – губчатое железо
- ГБЖ – горячебрикетированное железо
- Наиболее часто встречающиеся:
- DRI – процессы и продукты производства «бескоксовой» металлургии
- SI, SPI (ГЖ) – продукт твердофазных процессов
- HBI (ГБЖ) – брикетированный продукт твердофазных процессов
В общем виде схема производства металлизованного продукта приведена ниже:
Классификация новых процессов производства железа
По виду используемого восстановителя новые процессы классифицируются по следующим группам:
I. Природный газ
- шахтная установка непрерывного действия (Midrex, Armco, Purofer, HYL-III);
- шахтная установка периодического действия – реторта (HYL-I, HYL-II);
- агрегат с кипящим слоем.
II. Природный газ + уголь
- вращающаяся трубчатая печь, шахтная установка (ITmk3).
III. Уголь
- одностадийные (Romelt);
- многостадийные (Corex, Finex, Hismelt, DIOS).
Для процессов I и II групп характерен твёрдый металлизованный продукт, процессы III группы производят жидкий полупродукт. Как уже говорилось выше, распространённость процессов III группы очень ограничена (5...6%), поэтому дальнейшее изложение будет касаться аспектов производства и использования твёрдых металлизованных продуктов.
Развитие технологий производства металлизованного полупродукта
Развитие процессов прямого восстановления идёт параллельно в двух направлениях: с одной стороны увеличивается количество реализованных проектов по технологии Midrex с использованием природного газа в качестве источника восстановителей, с другой стороны – развиваются процессы, основанные на конверсии углей. Наиболее популярна эта технология в Индии – государстве со значительными запасами железной руды и угля и с одним из самых незначительных удельных объёмов потребления стали (51 кг/человека), что делает её перспективной в отношении развития металлургического сектора.
Развитие процессов прямого восстановления железа (% от общего объёма производства DRI)
2005 | 2010 |
Особенности производства твёрдого металлизированного продукта
Технологическая схема производства металлизованного продукта предъявляет определённые требования и накладывает некоторые ограничения на используемое сырье:
<tr">
Процесс металлизации проводится в агрегатах с противотоком твёрдых материалов и газов.
Необходимость окускования исходных материалов для улучшения газопроницаемости шихты.
Причина |
Следствие |
Восстановление происходит в твёрдом виде без образования жидких продуктов плавки и отделения пустой породы в виде шлака. |
Ограничение по содержанию пустой породы в исходном материале. Для производства DRI требуется высококачественное кусковое железорудное сырьё с минимальным содержанием пустой породы. |
Восстановление происходит в твёрдом виде, т.е. проходит без удаления примесей. |
Ограничение по содержанию нежелательных примесей в исходном материале. Природное сырье должно содержать минимум примесей и нежелательных элементов. |
Отсутствие крупнокусковых разрыхлителей в агрегате металлизации. |
Необходимость обеспечения нормального газодинамического режима ведёт к необходимости снижения диаметра агрегатов. Негативным результатом этого является снижение удельной производительности агрегатов. |
Продуктом является пористое свежевосстановленное железо, находящееся в восстановительной среде внутри агрегата металлизации. |
Возникают условия для сваривания частиц материала внутри агрегата. Для снижения эффекта необходимо снижение температурного уровня процесса, что приводит к снижению удельной производительности. |
Продуктом является пористое свежевосстановленное железо, находящееся в окислительной среде вне агрегата металлизации. |
Высокая площадь контакта с кислородом воздуха в малом объёме приводит к пирофорности – возможности самовоспламенения. Для снижения этого негативного эффекта необходима пассивация: обработка нейтральными веществами, хранение и перевозка в нейтральной среде, брикетирование. |
Таким образом, основными недостатками новых процессов производства железа являются:
- низкая удельная производительность агрегатов;
- необходимость использования шихты с высоким содержанием железа и низким содержанием пустой породы и примесных элементов;
- высокая потребность в энергоносителях и кислороде;
- высокие требования к условиям хранения и транспортировки.
Страны-производители DRI
Условия целесообразности строительства установок по производству DRI:
- относительно малая потребность внутреннего рынка в стали;
- малые ресурсы металлического лома и коксующихся углей;
- значительные ресурсы железной руды и природного газа.
Установки внедоменного получения железа сооружаются, в основном, в развивающихся странах, которые отвечают перечисленным выше условиям: Индия, Венесуэла, Иран, Мексика, Саудовская Аравия. Динамика производства DRI в разбивке по странам приведена на диаграммах.
Динамика производства DRI
Производство DRI в 2010 г.
Стоимость greenfield-проекта по производству DRI в объёме 2 млн. т в год оценивается в $350...$500 млн. Основные параметры проекта:
Объем производства |
2 млн. т в год |
Потребление природного газа |
700 млн. м куб. в год |
Потребление электроэнергии |
225 кВт×ч на тонну продукта |
Качество металлизованного сырья, новый металлизованный продукт - HBI
Производимые DRI отличаются высокими качественными характеристиками:
Показатель |
Содержание, % |
Feобщ |
92 ÷ 94 |
Feмет |
84 ÷ 88 |
C |
0,8 ÷ 1,5 |
P |
0,025 ÷ 0,045 |
S |
0,005 ÷ 0,030 |
SiO2+CaO+MgO+Al2O3 |
3,0 ÷ 6,5 |
Cu+Ni+Mo+Sn |
до 0,050 |
Выше отмечалось, что губчатое железо ввиду большой площади поверхности склонно к пирофорности в результате окисления на открытом воздухе. Даже если не происходит самовозгорания, то в результате окисления активного свежевосстановленного железа происходит снижение содержания железа и потеря металлургической ценности DRI. Динамика изменения содержание Fe в губчатом железе, хранящемся на открытом воздухе, приведена на диаграмме.
Поведение SPI при хранении
Для снижения пирофорности и улучшения насыпных и утилизационных характеристик DRI применяют технологию брикетирования в горячем состоянии. В результате брикетирования улучшаются физические (насыпной вес), логистические (хранение, транспортировка) и технологические (удобство использования в электропечах) характеристики DRI. Характеристики брикета:
Размер брикета, мм |
110 x 50 x 30 |
Вес, кг |
0,5 |
Насыпная масса, т/м3 |
2,4 ÷ 2,8 |
Эффекты брикетирования:
- увеличение насыпного веса в 1,3...1,8 раза;
- увеличение плотности в 1,4...1,6 раза;
- снижение химической активности (пирофорности) на порядок;
- удобство использования в ДСП (снижение времени загрузки, расположение на границе шлак-металл).
Мировое производство и перевозки металлизованного полупродукта
Динамика производства DRI с 1970 г. приведена на диаграмме.
Мировое производство DR
Объем мировой торговли DRI по видам продукта
Доля перевозимого DRI от его производства
Преимущества и недостатки использования DRI в EAF
Основным потребителем DRI является электросталеплавильное производство – доля DRI в металлошихте может достигать 70%. При этом DRI обладает определёнными преимуществами относительно других компонентов шихты:
- стабильность химсостава;
- низкое содержание нежелательных примесей (сера, фосфор);
- отсутствие сопутствующих элементов (свинец, медь);
- простота хранения, погрузки/выгрузки, транспортировки;
- высокая насыпная плотность;
- возможность подачи в электропечь без остановки процесса плавления;
- габаритное сырье гарантирует сохранность электродов от механических повреждений.
Но использование DRI в электропечах имеет свои недостатки:
- увеличение расхода электроэнергии (каждые 10% DRI: +15 кВт•ч/т стали);
- увеличение удельного расхода электродов (каждые 10% DRI: +0,2 кг/т стали);
- снижение выхода годного (каждые 10% DRI: –0,4 % объёма производства);
- увеличение времени плавки и снижение производительности (каждые 10% DRI: +2,5 минуты);
- увеличение тепловой нагрузки на футеровку в начале процесса.
Эти особенности применения DRI в качестве компонента шихты электрометаллургического производства находят отражение в стоимости DRI.
Справедливая цена DRI
При замещении 30% лома на DRI с аналогичной стоимостью удельные затраты при производстве стали растут на $8/т (см. диаграмму).
Для выполнения условия равенства затрат на 1 т выплавляемой стали цена DRI должна быть меньше цены высококачественного лома на 7%.
Эта оценка подтверждается фактическими данными – исторически цена DRI ниже цены металлолома в среднем на 5% (максимальное отклонение -13%):
Динамика цен DRI и металлолома
Следует отметить, что DRI является прямой альтернативой только для высококачественного лома сравнимого качества и типоразмера. При отсутствии достаточного количества высококачественного лома производство стали сравнимого качества возможно только при условии вовлечения металлизованного сырья.
Таким образом, новые технологии производства железа нашли свою нишу в современной металлургии и могут играть значительную роль в регионах с подходящими для их развития условиями.
- Неделин Сергей Васильевич Адрес электронной почты защищен от спам-ботов. Для просмотра адреса в вашем браузере должен быть включен Javascript.
Мартеновский процесс, долгое время державший монополию в области производства стали, уступил в конце 60-х годов XX века место более производительному кислородно-конвертерному. Дальнейшая борьба шла уже между конвертерным и набирающим силу электросталеплавильным процессом.
- производство стали;
- мартеновский процесс;
- кислородно-конвертерное производство;
- электросталеплавильный процесс;
- чугун;
- лом черных металлов;
- металлизованное сырье;
- Direct Reduction Iron (DRI).